-
Инспекция кранов и другого грузоподъемного оборудования от UGS — это обеспечение безопасности и надежности оборудования и соответствия установленным требованиям
Независимо от того, владеете вы кранами и другим грузоподъемным оборудованием или просто используете его, неободимо обеспечить его безопасность и соответствие установленным требованиям. В этом вам поможем мы!
- Погрузочно-разгрузочные механизмы:краны, деррик-краны, вильчатые погрузчики, автокраны, грузоподъемные серьги и крюки, подъемные платформы, телескопические погрузчики и т.п.
- Механизмы для транспортировки пассажиров:лифты, эскалаторы, подъемники для лыжников, фуникулеры и передвижные подъемные платформы (MEWP).
Инспекция кранов и другого грузоподъемного оборудования включает в себя:
- проверку тормозов, сцепления, осей и тросовых конструкций;
- разработку технических проектов и анализ расчетов;
- испытания с динамической и статической нагрузкой;
- инспекцию всех несущих элементов строительной конструкции, в том числе осей;
- проверку подкрановых балок, реек и стоек мостовых кранов для обеспечения прочности конструкции;
- проверку подвесного уровня и подкрановых путей;
- испытания неразрушающими методами (NDT) грузовых крюков на трещины и визуальный осмотр на деформацию;
- эксплуатационные испытания для подтверждения правильной работы узла;
- периодические инспекции и инспекции перед использованием механических, конструктивных, электрических систем и систем безопасности, а также тросов и цепей;
- повторную экспертизу всех защитных устройств;
- оценку нормативно-правового соответствия;
- оценку остаточного срока службы;
- надзор за проведением ремонтных работ;
-
Методика визуально-измерительного контроля сварных швов применяется при:
- проверке состояния подготовки и монтажа заготовок перед началом сварных операций.
- проверке качества швов в процессе сварки;
- определении состояния некоторых сварных соединений.
Проведение визуально измерительного контроля сварных соединений не зависит от применения других методик контроля. Во многих случаях внешний осмотр позволяет получить достаточно данных, при этом требует наименьших экономических, трудовых и временных затрат.
Визуальный измерительный контроль (ВИК) позволяет обнаружить различные дефекты – несплошности, отклонения размеров и форм более чем на 0,1 мм при условии применения оптических приборов с десятикратным или менее увеличением. Чаще всего контроль производится без оптики или с увеличительной лупой 7х. При технической диагностике и в особо сложных случаях применяются оптические средства с двадцатикратным увеличением.
Визуально-измерительный контроль сварных швов требует тщательной предварительной подготовки поверхности. Необходима очистка от грязи, ржавчины, краски, брызг металла и других загрязнений, препятствующих контролю. Зоной контроля при ВИК является сам сварной шов, а также прилегающие участки металла шириной от 20 и более миллиметров. Производится осмотр обеих прилегающих к шву сторон при условии наличия возможности их осмотра. Применение всех прочих методик производится после визуально-измерительного контроля. Только после устранения всех обнаруженных при ВИК основных дефектов сварного шва или при их отсутствии производится углубленные исследования другими средствами.
Визуально измерительный контроль сварных соединений производится с помощью следующих средств:
- измерительных линеек;
- увеличительных измерительных луп кратностью до 10 – 20 х;
- штангенциркулей;
- угломеров и угольников;
- щупов, шаблонов и других средств измерения требуемой точности.
Сфера применения визуально измерительного контроля (ВИК) охватывает следующие технологические операции:
- При технической диагностике ВИК необходим для определения наличия и размеров отклонений геометрической формы и размеров конструкции от проектных значений, наличия дефектов в основном металле и сварном шве.
- Входной контроль материалов перед сварочными операциями. Определяется наличие и характер поверхностных дефектов (забоин, раковин, трещин, включений шлака и т. д.), отклонений от геометрических размеров заготовок.
- Подготовка элементов сварных конструкций. ВИК необходим для контроля точности геометрических размеров, соответствия чистоты кромок проектным требованиям, изучения состояния прилегающих поверхностей. Также производится контроль угловых и поверхностных смещений, зазоров между деталями, качества, местоположения и количества произведенных прихваток.
- В процессе или по завершению сварки – выявляется наличие дефектов и несплошностей, таких как прожоги, наплывы, подрезы, раковины, трещины и т. д. Также при ВИК определяются отклонения геометрических размеров сварного шва от установленных требований в проектной и нормативной документации.
Основные преимущества методики ВИК
Внешний контроль качества сварного шва визуальным методом является наиболее простым и, вместе с тем, очень эффективным способом обнаружения различных видов дефектов. Его применение позволяет значительно сэкономить время и деньги, не проводить более дорогостоящие и затратные по времени исследования (рентген, ультразвук, капиллярный контроль и т. д.) до устранения заметных при визуальном контроле дефектов. Только после ВИК и устранения обнаруженных дефектов проводятся другие методы контроля.
К сожалению, нередко ВИК не уделяется достаточно внимания, и вспоминают о нем лишь на завершающих этапах работ, когда проведение исследований либо затруднено, либо невозможно в силу технических причин. Такое отношение может привести к серьёзным последствиям, авариям и техногенным катастрофам.
-
Одним из современных и наиболее часто используемых методов неразрушающего контроля целостности металла и сварных швов трубопроводов и других металлических изделий является УЗК – ультразвуковой метод контроля. Суть ультразвукового метода неразрушающего контроля – это излучение и прием отраженного ультразвукового сигнала с помощью специального оборудования: ультразвукового дефектоскопа и пьезоэлектрического преобразователя. Полученный отраженный сигнал анализируется на наличие дефектов и, в зависимости от времени распространения ультразвука, амплитуды импульса и пр. факторов, определяется их размер, форма, вид, глубина залегания и пр. параметры.
Компания «Полиинформ» проводит ультразвуковой контроль сварных соединений и целостности металла с помощью современных приборов – дефектоскопов, генерирующих излучение в диапазоне до 20 МГц. Чем выше частота, тем меньший размер дефектов можно уловить с помощью прибора. Малые частоты применяются для исследования объектов большой толщины или с крупнозернистой структурой.
Преимущества и недостатки ультразвукового контроля
Основными преимуществами данной методики является использование ультразвуковых волн в качестве инструмента исследований. В частности, неразрушающий ультразвуковой контроль обеспечивает:
- высокоточное исследование при минимальных затратах времени;
- малую стоимость диагностики;
- безопасность для персонала благодаря отсутствию вредных излучений;
- высокую мобильность благодаря применению портативного оборудования;
- возможность проведения исследований на действующих объектах, при проведении УЗК не требуется останавливать транспортировку сред по трубопроводу;
- сохранение целостности исследуемого объекта.
Основные недостатки метода:
- Невозможность определения некоторых дефектов в силу их характера, формы или расположения, заполненности тем или иным материалом.
- Сложности с определением реального размера дефекта, возможность определения только эквивалентного размера.
- Сложности при УЗК металлических изделий с крупнозернистой структурой.
- Необходимость тщательной очистки поверхности перед проведением контроля.
Особенности ультразвукового контроля
Ультразвуковая дефектоскопия, так же как и другие физические методы – магнитно-порошковая дефектоскопия, рентгенографические исследования и т. д., является наиболее надежным и высокоэффективным методом исследования. Исследование должно производиться высококвалифицированными специалистами, оснащенными современным оборудованием и вспомогательными средствами контроля. Для ультразвуковой дефектоскопии также необходима тщательная подготовка поверхности исследуемого объекта.
Следует особо отметить, что проведение УЗК должно производиться на различных стадиях подготовки объекта, а не только непосредственно перед его сдачей, когда контроль сопряжен со значительными трудностями, а иногда и технически невыполним. Неразрушающая диагностика – обязательный этап ввода трубопроводов, котлов и других объектов в эксплуатацию, важный фактор предотвращения аварийных ситуаций и техногенных катастроф.
-
Магнитопорошковая дефектоскопия (МПД) – это метод неразрушающего контроля предназначенный для определения мелких дефектов в поверхностной и подповерхностной структуре металла, проходящих внутрь изделия. Данный метод эффективен в определении трещин, надрывов, волосовин, непроваров, пор и других дефектов.
Технология метода магнитопорошковой дефектоскопии
Основой метода является притяжение магнитного порошка выходящим на поверхность объекта магнитным потоком. Наличие дефектов в ферромагнитном объекте вызывает отклонение силовых линий магнитного поля, создание местных магнитных полей рассеяния и локальных магнитных полюсов и, соответственно, изменения в движении порошка.
Магнитопорошковая дефектоскопия состоит из следующих этапов:
- Предварительная подготовка поверхности, очистка от ржавчины и загрязнений.
- Намагничивание исследуемой поверхности.
- Нанесение на поверхность мелкодисперсного ферромагнитного порошка.
- Визуальное изучение поверхности и фиксация образованных индикаторных рисунков.
- Размагничивание поверхности.
Мелкодисперсный магнитный порошок вовлекается в сферу действия образованных локальных магнитных полюсов и растекается по поверхности изделия, образуя валики по форме трещин и иных дефектов. В магнитопорошковой дефектоскопии используется сухой и мокрый способы нанесения порошка. Как правило, для грубообработанных или необработанных поверхностей используется сухой метод. Контроль изделий с высоким классом шероховатости производится посредством суспензии из мелкодисперсного порошка на основе масла или керосина.
Для улучшения видимости при магнитопорошковом методе неразрушающего контроля в порошок добавляется двуокись титана или окись цинка для придания ему серого цвета. Также применяется контроль с помощью ультрафиолетового излучения, для чего используется специальный люминесцентный магнитный порошок.
Преимущества магнитопорошковой дефектоскопии
Магнитопорошковый метод неразрушающего контроля относится к наиболее перспективным и эффективным направлениям анализа и измерений в металлургии, машиностроении, нефте- и газовой промышленности. Он широко применяется при контроле состояния трубопроводов горячей и холодной воды, газо- и нефтепроводов, позволяет производить оценку и диагностику структуры материалов.
К основным преимуществам магнитопорошковой дефектоскопии можно отнести:
- Сравнительно небольшие трудоемкость и временные затраты на проведение диагностики.
- Высокая точность метода, возможность обнаружения поверхностных и подповерхностных дефектов.
- Одинаковая эффективность в выявлении как полых дефектов, так и несплошностей заполненных другими веществами, например водой, нефтью или пылью.
- Возможность эффективного поиска усталостных трещин, возникающих в ходе эксплуатации объекта.
По данному направлению компания «Полиинформ» предлагает проведение полного комплекса исследований различных объектов как с применением МПД, так и в комплексе с другими технологиями неразрушающего контрол
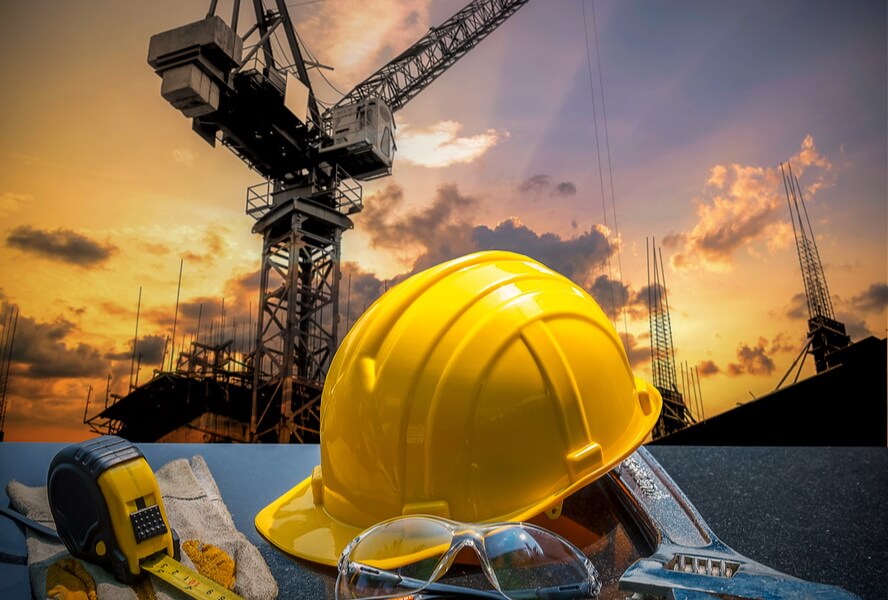